Manufacturing Order
Overview
The Manufacturing Order (MO) feature is designed to plan, coordinate, and control various aspects of the production process to ensure efficient and effective manufacturing operations. This feature allows you to outline the specific details and instructions required to produce a particular product in an organized manner.
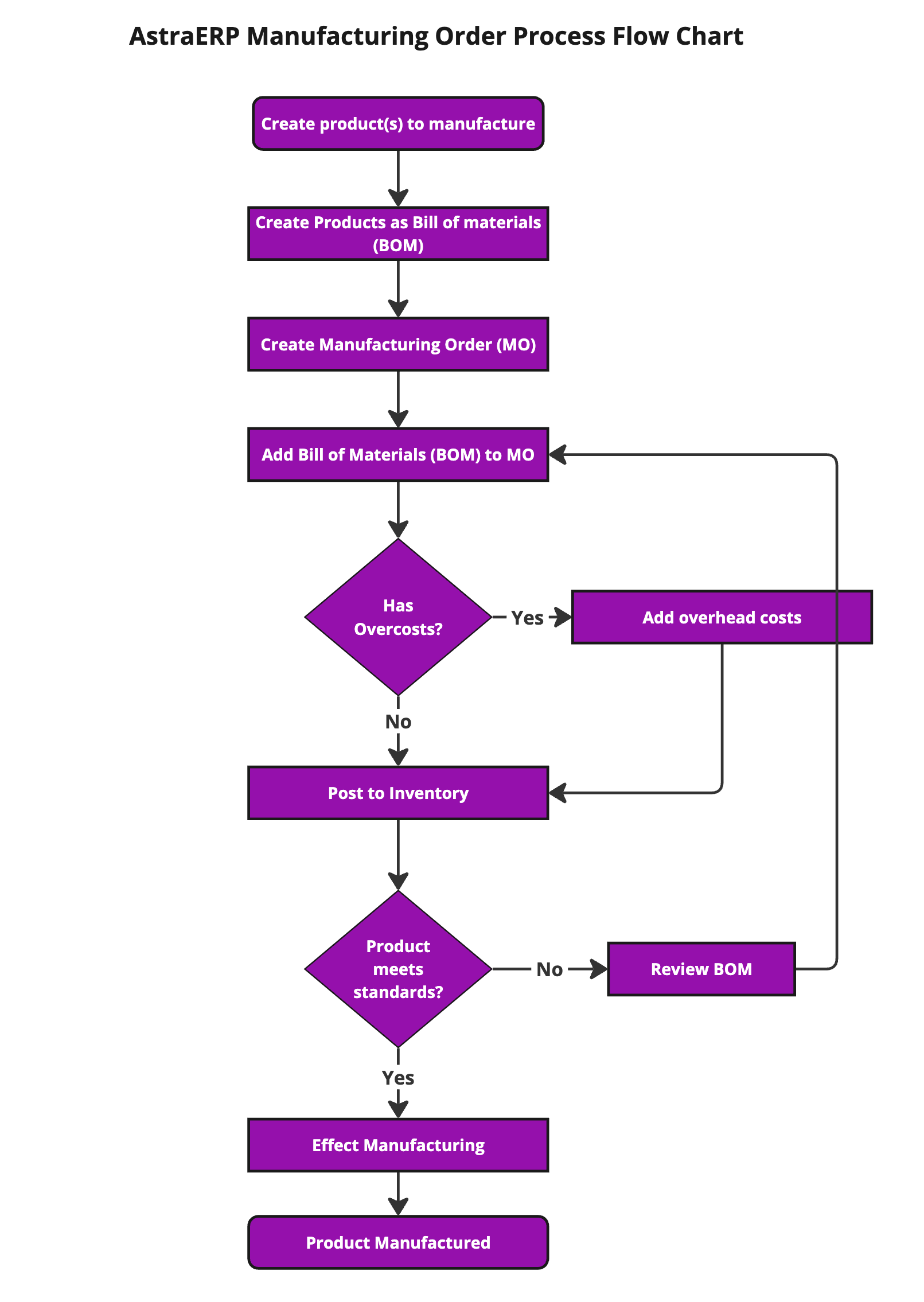
Key Components and Functions
- Location: The location where the product will be manufactured.
- Batch Number: A unique identifier assigned to the Manufacturing Order.
- Memo: A brief note or description about the product being manufactured.
- Transfer to Location after Manufacturing: This option is necessary if you have designated separate locations within the system for handling manufacturing and sales.
- Product: The product(s) to be manufactured. Only products that have been created with the label 'produce' can be selected.
- Quantity to Produce: The quantity of the product that is to be manufactured.
Creating a Manufacturing Order for Product(s)
To create a Manufacturing Order, follow these steps:
- In the Inventory Module, navigate to Manufacturing > Manufacturing Order.
- Enter the required data for the following fields:
- Location: Specify the manufacturing location.
- Order Date: Enter the date for the manufacturing order.
- Batch Number: Provide a unique batch number for the order.
- Memo: Add any relevant notes or descriptions.
- Product: Select the product(s) to be manufactured.
- To save the Manufacturing Order, click the Save and Continue button.
- After successfully saving the order, the Manufacturing Order listing page will open.
- New Manufacturing Orders have the Order Status of Planning.
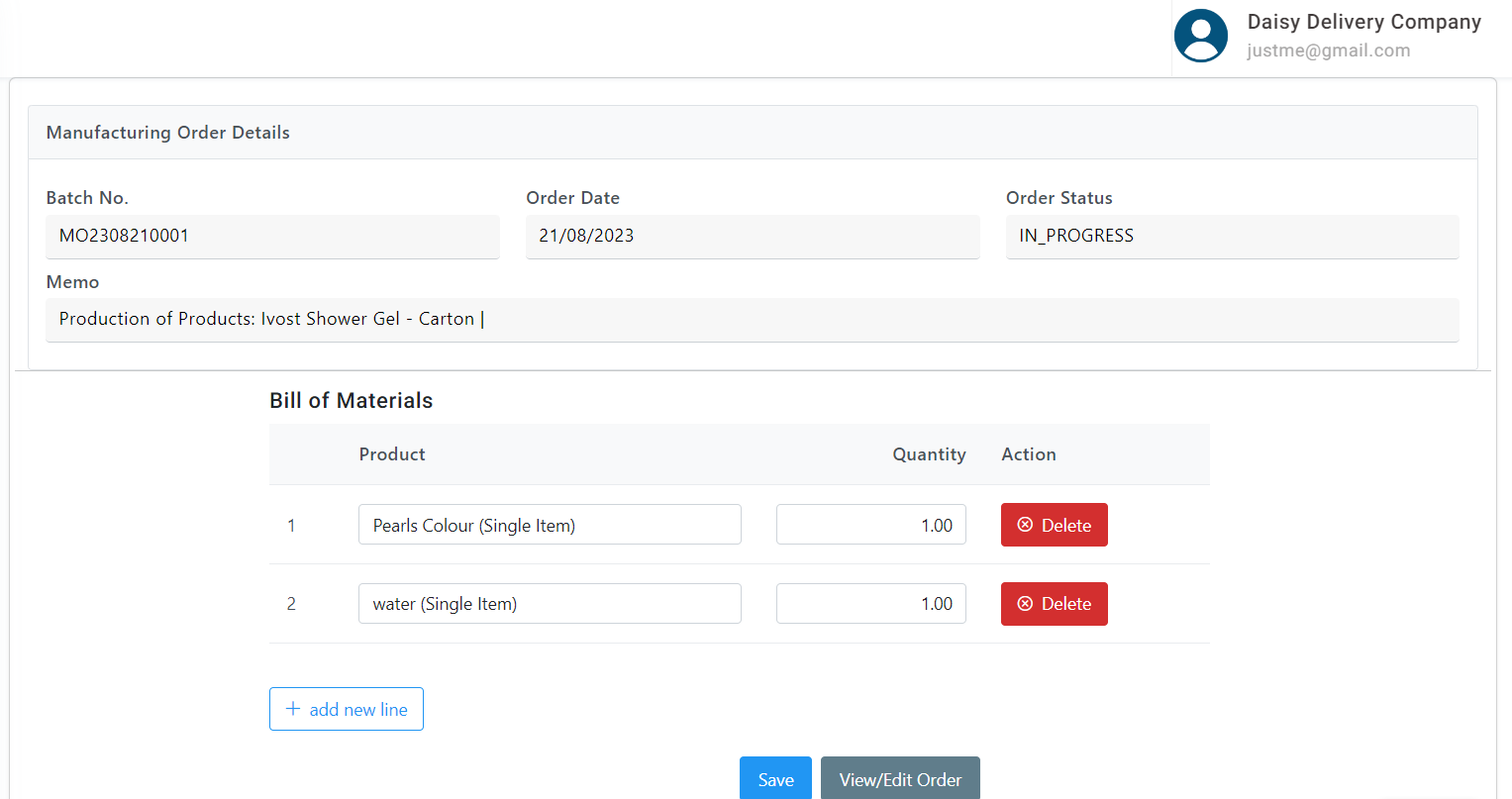
Editing a Manufacturing Order
To edit an existing Manufacturing Order:
- On the Manufacturing Order listing page, locate the order you want to edit.
- Click the Edit button next to the Manufacturing Order.
- Modify the fields as needed, such as Location, Order Date, Batch Number, Memo, or Product.
- After making the necessary changes, click the Save and Continue button to update the Manufacturing Order.
- The updated Manufacturing Order will be reflected in the listing page with the changes applied.
Bill of Materials (BOM)
Overview
The Bill of Materials (BOM) is a detailed list of all the raw materials required to manufacture the final product. It specifies the quantities of each item necessary to produce the order quantity specified in the Manufacturing Order.
Adding a Bill of Materials to the Manufacturing Order
To add a Bill of Materials to an existing Manufacturing Order, follow these steps:
- On the Manufacturing Order listing page, click on the MO (Manufacturing Order) for which the BOM needs to be added.
- You will be directed to the BOM page. Here, you can add the required raw materials and any associated costs:
- Select Product (Raw Material): Choose the raw material that will be used in the manufacturing process.
Only products labelled Buy/Sell can be selected. When the product(s) are tracked, there should be enough stocks for the product.
- Add Quantity Needed: Enter the quantity of the selected raw material required for the production.
- Select New Line to Add More Products (Raw Materials): Continue adding raw materials by selecting a new line for each additional product.
- Overhead Costs: If applicable, add any overhead costs associated with the manufacturing process, such as:
- Labour
- Water
- Electricity
- Others
- Once all the required information is entered, click Save to add the Bill of Materials to the Manufacturing Order.
Post to Inventory
Overview
Posting to Inventory is the final step in the manufacturing process. This action updates the stock levels to reflect the completion of the manufacturing process and the availability of the final product.
Steps to Post to Inventory
- On the Manufacturing Order listing page, locate the Manufacturing Order (MO) that has completed the manufacturing process.
- Click on Post to Inventory next to the relevant MO.
- You will be directed to a review page. Carefully inspect the details, including the MO products and the Bill of Materials (BOM).
- Once you are satisfied with the reviewed information, click on Effect Manufacturing to complete the process. This action will update the inventory levels to include the newly manufactured products.
Status Tracking
Overview
Throughout the manufacturing process, the status of the Manufacturing Order (MO) is updated to reflect its progress. This status tracking helps in monitoring and managing the different stages of production.
Status Information
Planning/Pending Order:
- This initial status indicates that the Manufacturing Order has been created and is awaiting the start of the manufacturing process.
In Progress:
- The "In Progress" status indicates that the manufacturing order has been initiated, and the production process is currently ongoing.
Completed:
- The "Completed" status signifies that the manufacturing order has been fully processed and finished. The final product has been manufactured, and the stock levels have been updated accordingly.
Manufacturing Order Color Indicators
The Manufacturing Order (MO) listing page uses color labels to indicate the status or condition of each order:
- Pending Order: Light Blue
- Profit Margin Less Than 0%: Light Red or Pinkish Red
- Profit Margin Greater Than 100%: Light Yellow